Typical House Construction Methods in Australia
Let's dive into the most popular residential construction systems in Australia
10/15/20237 min read
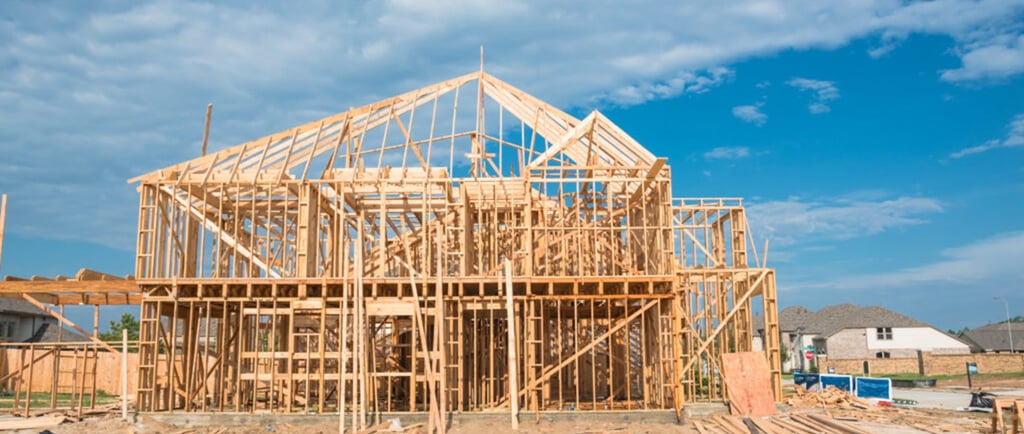
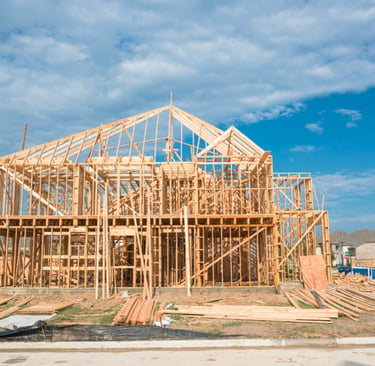
Let's begin with the most used construction method: timber framing. In Australia, it's called timber, while in the United States, it's referred to as wood framing. Timber framing is the most popular and affordable construction system for houses in Australia.
As an engineer, I find it essential to identify patterns when examining a structural system. By simply looking at an image of a timber framed house, it becomes apparent that it consists of numerous small timber elements working in parallel. For example, the roof rafters and wall studs function in parallel, with each element sharing the loads.
Timber framed house under construction
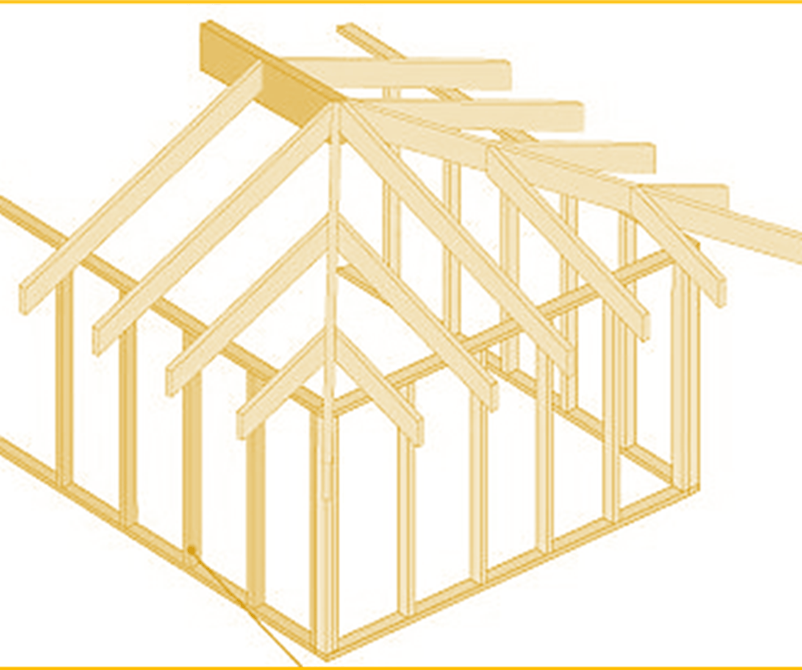
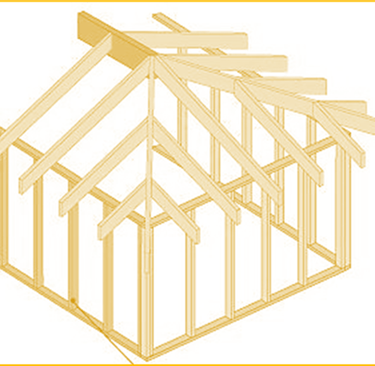
The wall framing is the skeleton of a wall in a house. It provides a stable structure that supports the weight of the house and live loads, transfer wind loads to the footings and diaphragms and also provide a framework for attaching wall coverings, such as drywall or siding. In terms of nomenclature, the wall frame comprises bottom and top plates, studs, jamb studs at each side of openings, noggings, tie-down steel rods and lintels/trimmers above openings.

Frame working in parallel.
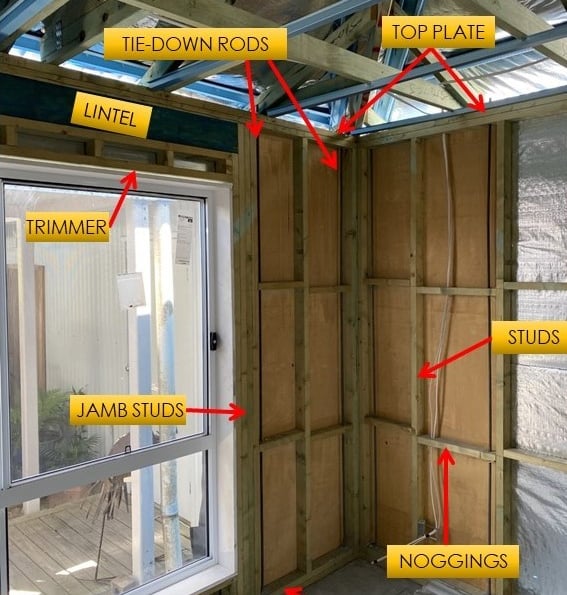
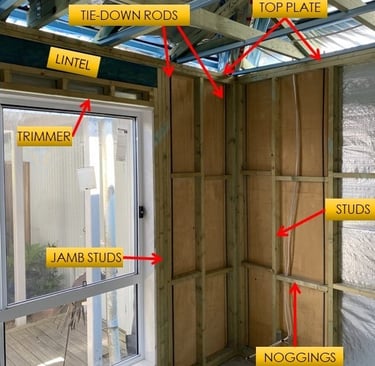
Basic wall framing elements.
Just as the wall framing is the skeleton of a wall in a house, the floor framing is the skeleton of the floor. It creates a stable structure that supports the weight of the structure, occupants, furniture and other loads. Besides that, the floor framing is also part of the diaphragm to distribute lateral loads. It consists mainly of joists landing on bearers and bearers landing on columns. Columns can be made of timber, concrete or steel as per the image below.
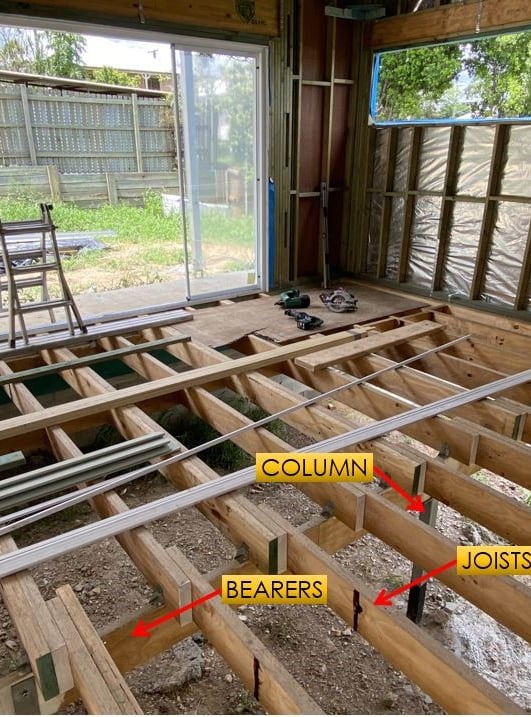
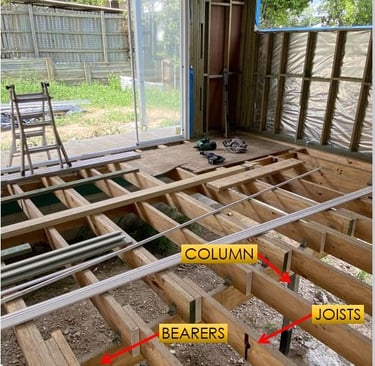
Basic floor framing elements.
Alternatively, the house can sit on a slab on ground, also known as slab on grade. A slab on ground is a common type of foundation used in construction. It is a flat, horizontal concrete structure that serves as both the foundation and the floor of a house.
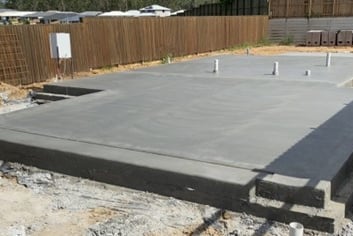
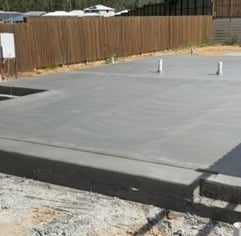
Slab on ground after concrete pour
The concrete slab is reinforced with steel mesh sitting on bar chairs. The thickness of the slab can vary depending on the load it needs to support and the specific requirements of the project, however they are usually 100mm thick (waffle pods are usually 85mm thick). A grid of ground beams is constructed to provide stiffness to the system.
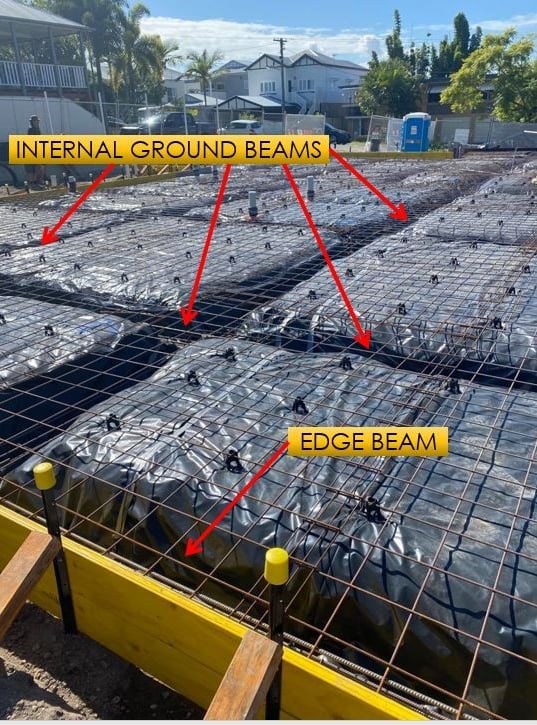
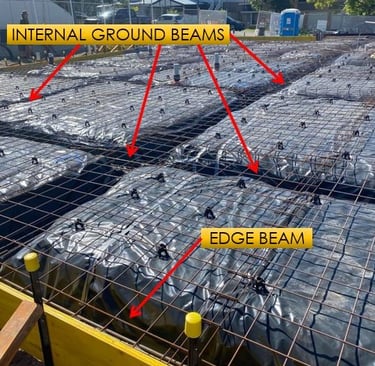
Slab on ground before concrete pour
Understanding the load paths is crucial. Gravity loads in a timber framed house are transferred from the roof down to the footings. This transfer occurs through the roof/ceiling, walls, floor, wall framing, and eventually to the footing. While this process may seem straightforward, comprehending the load paths is vital for a solid understanding of the structure.
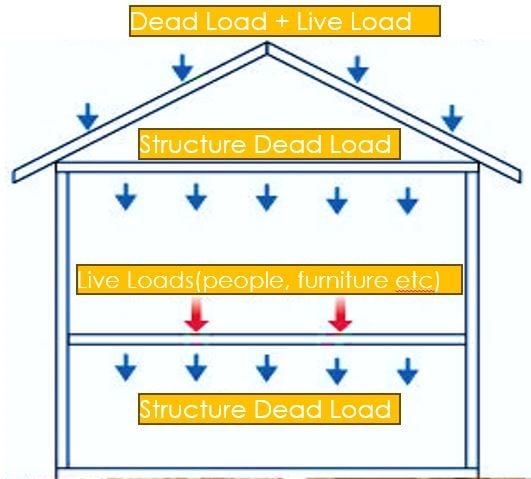
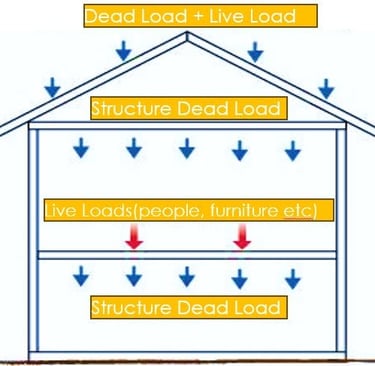
Gravity Loads diagram
Apart from gravity loads, there are lateral loads from wind. In cyclonic areas, wind gusts can reach over 300 kilometers per hour, similar to the speed of a Formula 1 car or a Ferrari.
Generally, the wind passes through the roof, ceiling, bracing walls, floor and footing as per the diagram below:
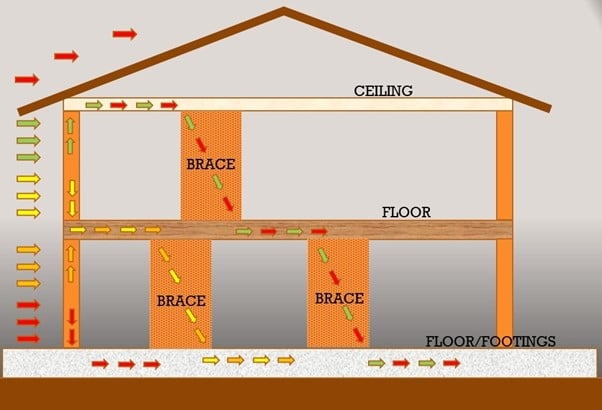
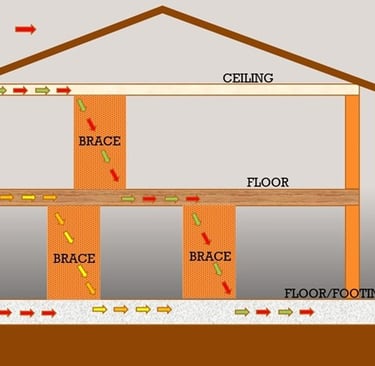
Wind load path simplified. Loads going through ceiling and floor diaphragm. Uplift pressure on roof and internal pressures not shown.
Engineers rely on standards such as AS1684, AS2870, AS1170, and AS4055 to design timber framed structures, ensuring compliance with safety regulations and industry standards.
The construction process for timber framed houses begins with preparing the foundation and footings, followed by sanitary drainage and concrete floors or bearers and joists.
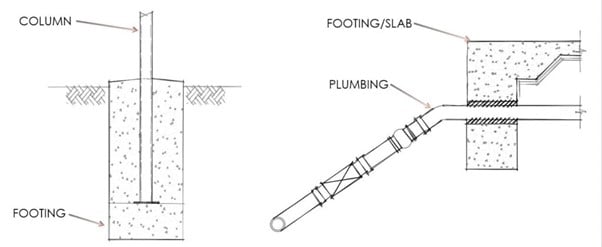
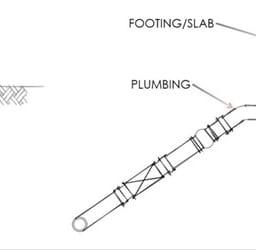
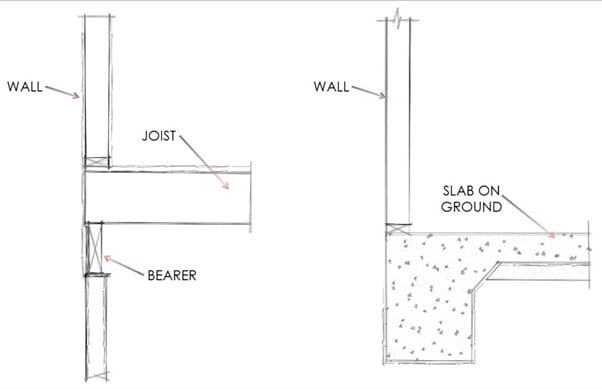
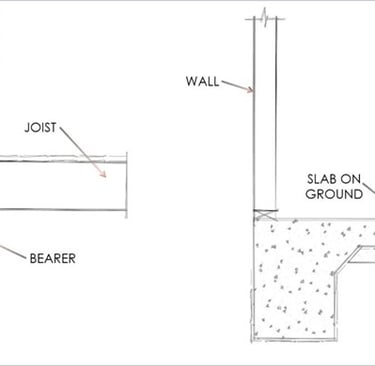
Then, the wall frame is erected, and subsequently, the roof framing is constructed. Windows, doors, plumbing pipes, electrical wiring and fixtures are installed.
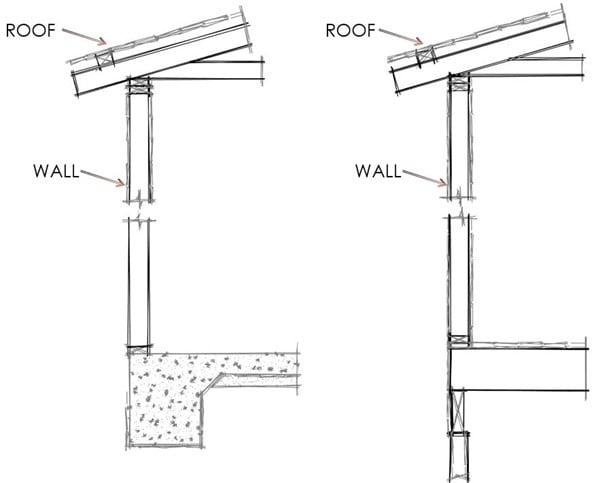
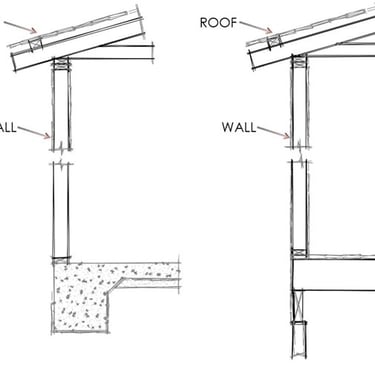
BRICK VENEER
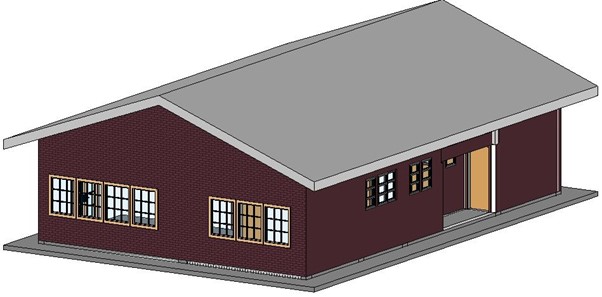
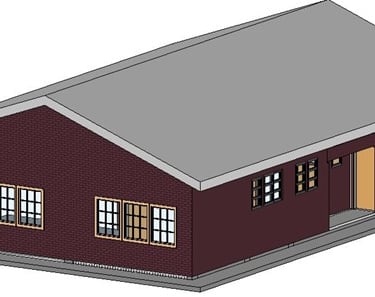
The second construction method is Brick Veneer. It involves a brick façade fixed to a timber framed wall.
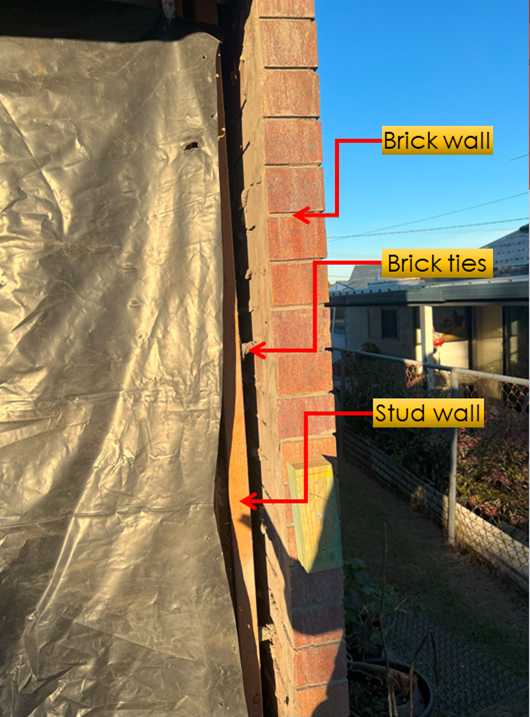
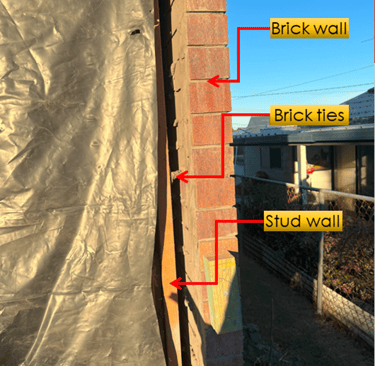
The brick is tied to the frame using brick ties, and a cavity of approximately 40 mm provides insulation and acts as a moisture barrier. The timber frame does wall the structural load bearing work, in other words, the stud wall is holding up the house, not the brick.
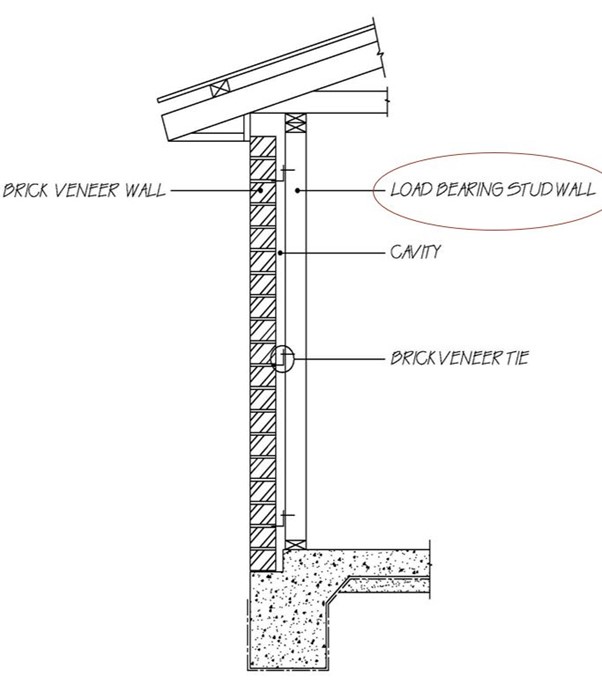
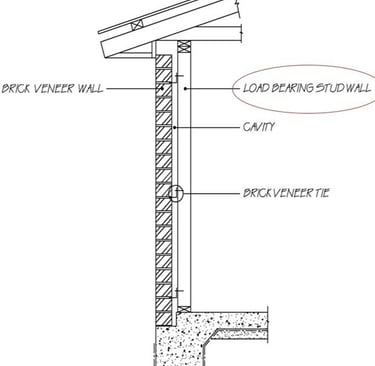
AS1684 and AS4773 are standards used for designing Brick Veneer houses, alongside the standards mentioned before. Construction stages include footings, sanitary drainage, laying the floor, erecting timber wall frames with bracings, constructing the roof framing, installing windows and doors, and finally, constructing the brick walls.
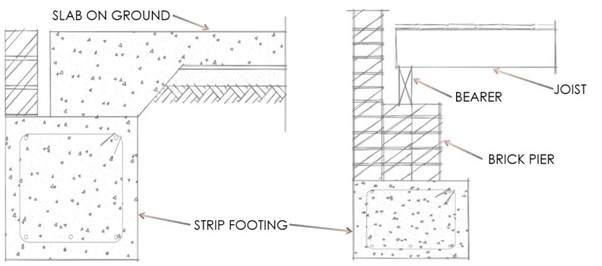
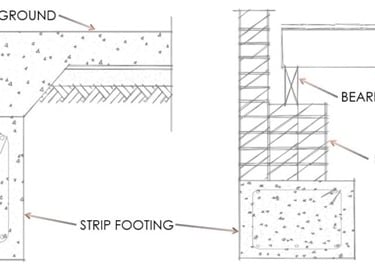
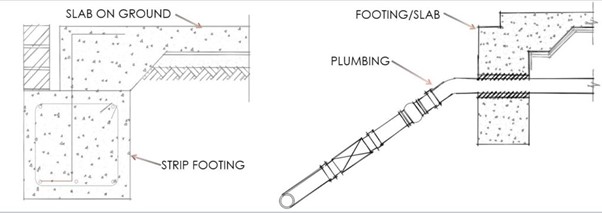
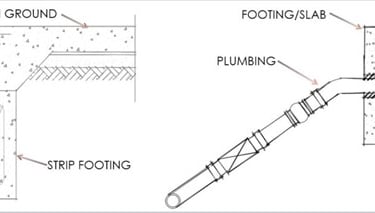
Slab on ground sitting on a footing on the left. Image on the right shows a monolithic slab on ground with pipe going through it.
Image on the left shows a slab on ground sitting on a footing again. Figure on the right shows a brick pier sitting on a footing. Joists are landing on a bearer, while the bearer is supported by the brick piers.
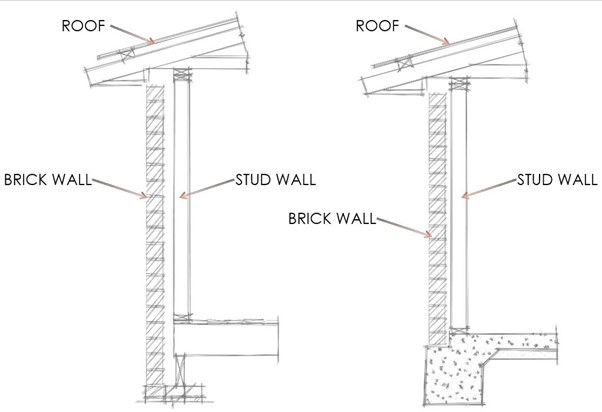
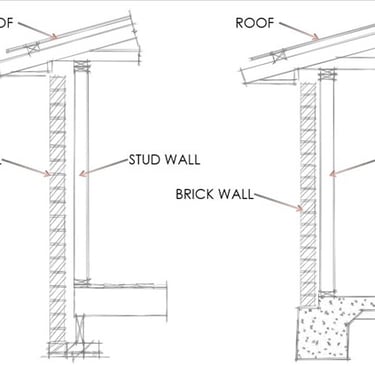
Figure shows a typical section of an external wall of a single-storey brick veneer house.
DOUBLE BRICK HOUSE
The third method is Double Brick construction, consisting of two brick walls standing side-by-side with a cavity between them. These walls are tied together using cavity ties.
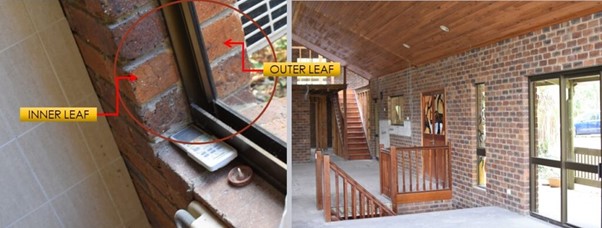
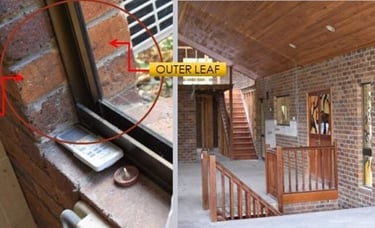
Internal partitions can be made of studs, brick, or concrete blocks, which can be rendered or lined with wallboard.
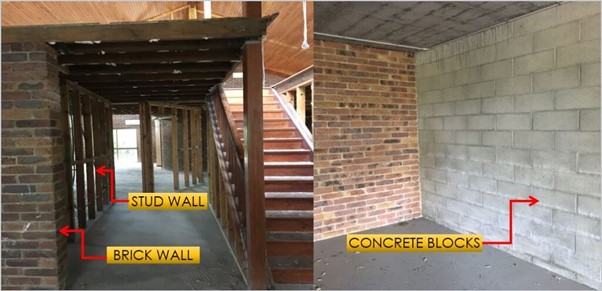
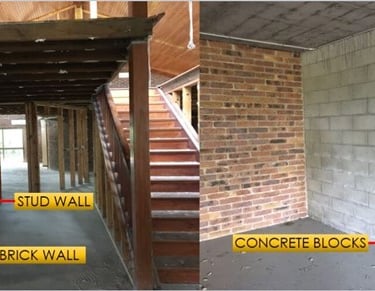
Designing Double Brick structures requires consideration of standards such as AS4773, in addition to other relevant regulations. The construction process involves laying reinforced footings, building the inner leaf of the double wall, constructing internal partitions, erecting the roof, and completing interior work while simultaneously building the outer brick leaf.
Possible solution for footings on a double brick construction.
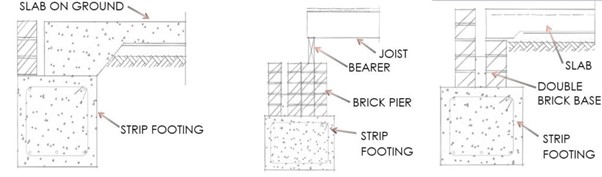

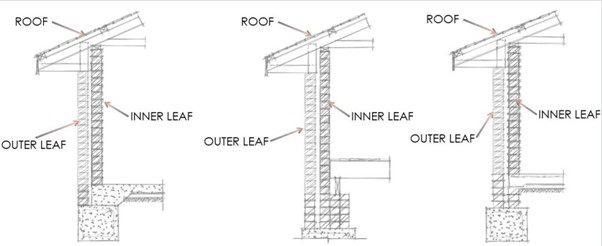
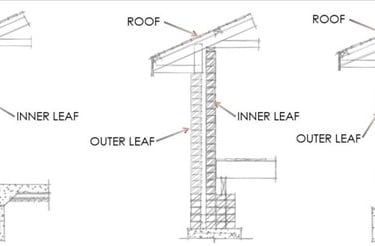
Figure shows a typical section of an external wall of a single-storey double brick house.
BLOCKWORK CONSTRUCTION
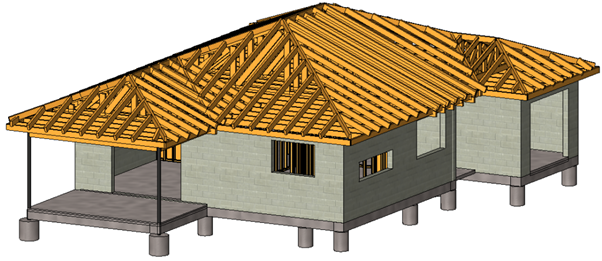
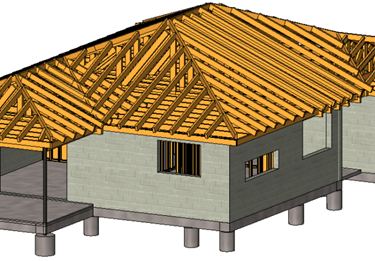
Moving on to Blockwork construction, which involves the use of concrete blocks for external walls and timber or blocks for internal partitions. External block walls are typically 190mm thick, while internal partitions can be constructed using timber or 90mm to 140mm blocks. Reinforced block walls may require the use of 140mm or 190mm blocks. For reinforced masonry walls, specific reinforcement measures are taken. Typically, N12 or N16 bars are used, placed in designated vertical cores, bond beams, and lintels.
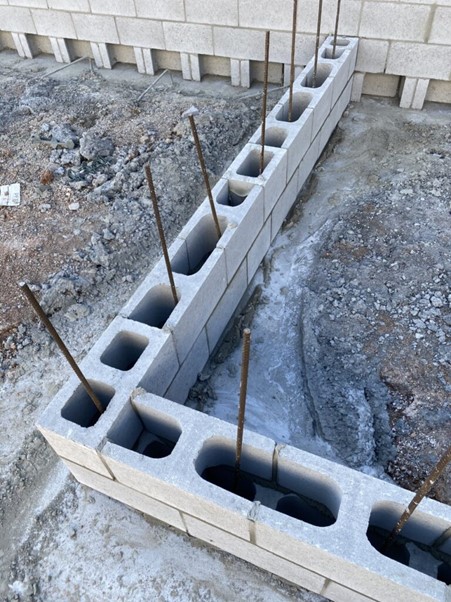
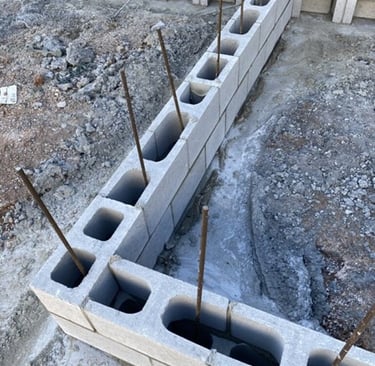
When designing Blockwork structures, engineers refer to standards such as AS4773, in conjunction with other relevant design guidelines provided by organizations like the Concrete Masonry Association of Australia.
The construction process for Blockwork structures begins with the construction of footings or any required blockwork below slab level for soil retention. Subsequently, the slab is prepared, incorporating relevant drainage systems and plumbing services. Blockwork construction follows, with the installation of reinforcement. Anchor bolts are also installed, specially designed for wind uplift.
Image shows first layers of block with N12 starter bars coming out of footing.
Possible solution for footings on blockwork construction.
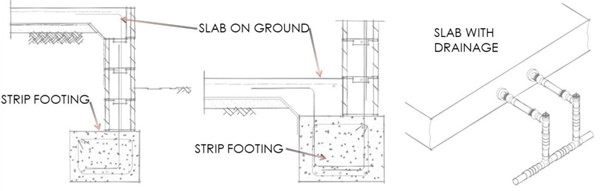
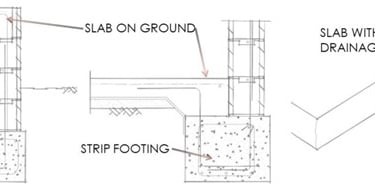
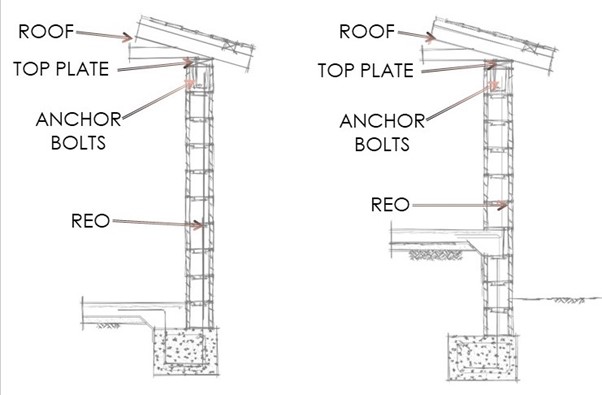
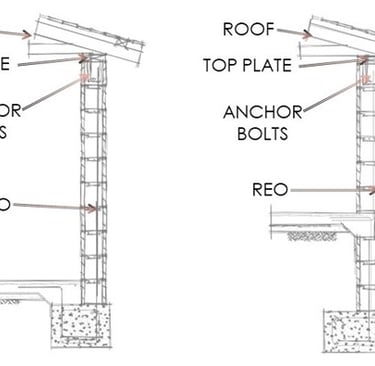
Figure shows a typical section of an external wall of a single-storey blockwork house
Next, plumbing and electrical conduits are installed, followed by the pouring of concrete into vertical cores, lintels, and bond beams. The construction process then progresses to fixing top plates if necessary, constructing internal partitions and roof framing, attaching sarking and cladding to the roof, rendering exterior walls if desired, and finally, installing windows, doors, and fixtures.
CONCLUSION
These construction methods represent some of the most popular techniques used in the country. The choice of construction method varies among states due to factors such as material availability, labor resources, climate considerations, and cost factors. Additionally, other construction systems such as reinforced concrete beams and columns, modular homes, light steel framed houses, and container houses are gaining popularity in the industry, offering a wide range of options to meet diverse needs and preferences.